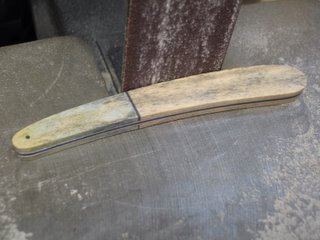
Back to the sanding process... Sand the profile of the
"single" scale, using all the work spots of the sanding belt as defined in the last section.
Don't forget that you can use the
leading as well as the
trailing edge of the sanding belt to remove everything that doesn't look like a set of scales. Go slow, especially with the rougher grits of sandpaper... remember, you can't put the material back once it is gone.
I did not have the machine running for the photos. Didn't want any mishaps. Notice how the gentle curve of the back can be easily sanded by turning it vertically.
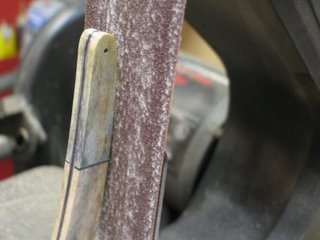
Before going to a finer grit paper, make sure you are completely done with the scales with the current grit. Then, progressively work your way to finer and finer grits. This is a good progression:
- 80 grit
- 220 grit
- 400 grit
- 600 grit
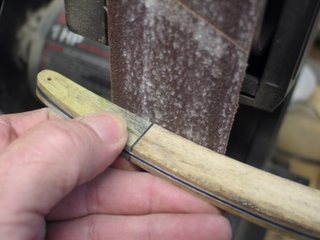
Much of my work is done freehand and by "eyeball" You can get pretty good at it with a little practice.
Do be careful when sanding your scales as illustrated on the left photo. That sanding belt has
no respect whatsoever for your fingers and knuckles.
It is about here that you will actually see why I said it was important to line the scales up at the dividing line of the materials. Lookin' good, eh?
I'm going to throw in a photo of another set of scales I was working on to illustrate how I use the upper contact wheel to finish the inside curves.
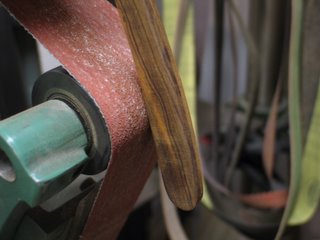
This area of the wheel is indespensible for all of the inside curves and edge bevels.
Once all of the profile is finished, you are practically done. It is time to address the edges of the profile.
I slope mine a tad like the gentle roofline of a toolshed, not just round them. It allows me to dome the sides to give a well rounded and pleasing contour.
You can also leave the edges relatively sharp and striking. Here is where you play around to develop your own style.
My knives are like that. When I was really active with them, people knew I made a specific knife simply because of the style. Most good knifemakers develop this attribute.
I use the sanding belts to round all of my edges, but I don't even go near them until I am down to 400 grit. Otherwise, you will remove too much material. Practice with a curved piece of wood before working on a set of scales with liners.
Practice being the key word.
After doing what you can with the machines, do the rest with files, rotary tools, and sandpaper. Have some patience... you will get down to this...
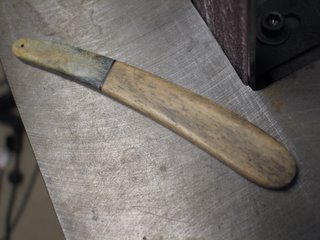
Buff the
"single" scale out. Once that is done, take a utility razor knife and carefully separate the two halves.
Use your thumb to roll the
rubber cement on the insides of the scales into a huge
booger. You can toss it in the trash can or play with it for a while like you did as a kid. Sand the insides lightly.
Seal the inside edges with thin superglue. Try not to get any on the outside of your new scales or glue your fingers to them like I did. Sand lightly with 1,000 grit paper. Take the burr off the inside edges of the scales with the same grit paper. Put renaissance wax over the whole kit and caboodle. Renaissance wax is expensive, but you will only need one jar and it works really great for scales and blades.
Here we are!
Wall Ah! Or, if you prefer...
violã. This concludes Making Scales 101. Next will be putting them on a blade. I guess that would be called Pinning Scales 101.
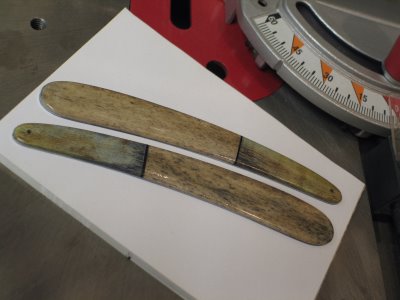
Addendum: Drill the holes except the one at the heel or butt all the way through on the one scale. Once that is done, put that scale on top of the other one. Make sure the two halves are lined up perfectly as they were before you separated them. Take it to the drill press and run the bit slightly through the holes you just made just to provide the starting point for drilling on the inside of the other scale. Separate them and finish drilling the holes, being very careful as the drill bit breaks through the material of the scales so they don't chip out. There should only be 3 holes drilled for now.
If you are interested in the pinning lessons, I need to know. Now is the time to make comments, not only for what I have already written, but for encouragement for me to continue. I need more than 5 or 10 of you to say something to put it here on this blog. No interest here and I'll just put it in the update on my CD.
Hope you have learned something. Send me pics of your projects...